Production Orders & Shift Tracking
Track your shifts and production orders
With TrendOEE, you can track production efficiency based on both shift changes and production orders. Get a clear overview of performance per shift and gain insights into how planned orders actually unfold in practice.
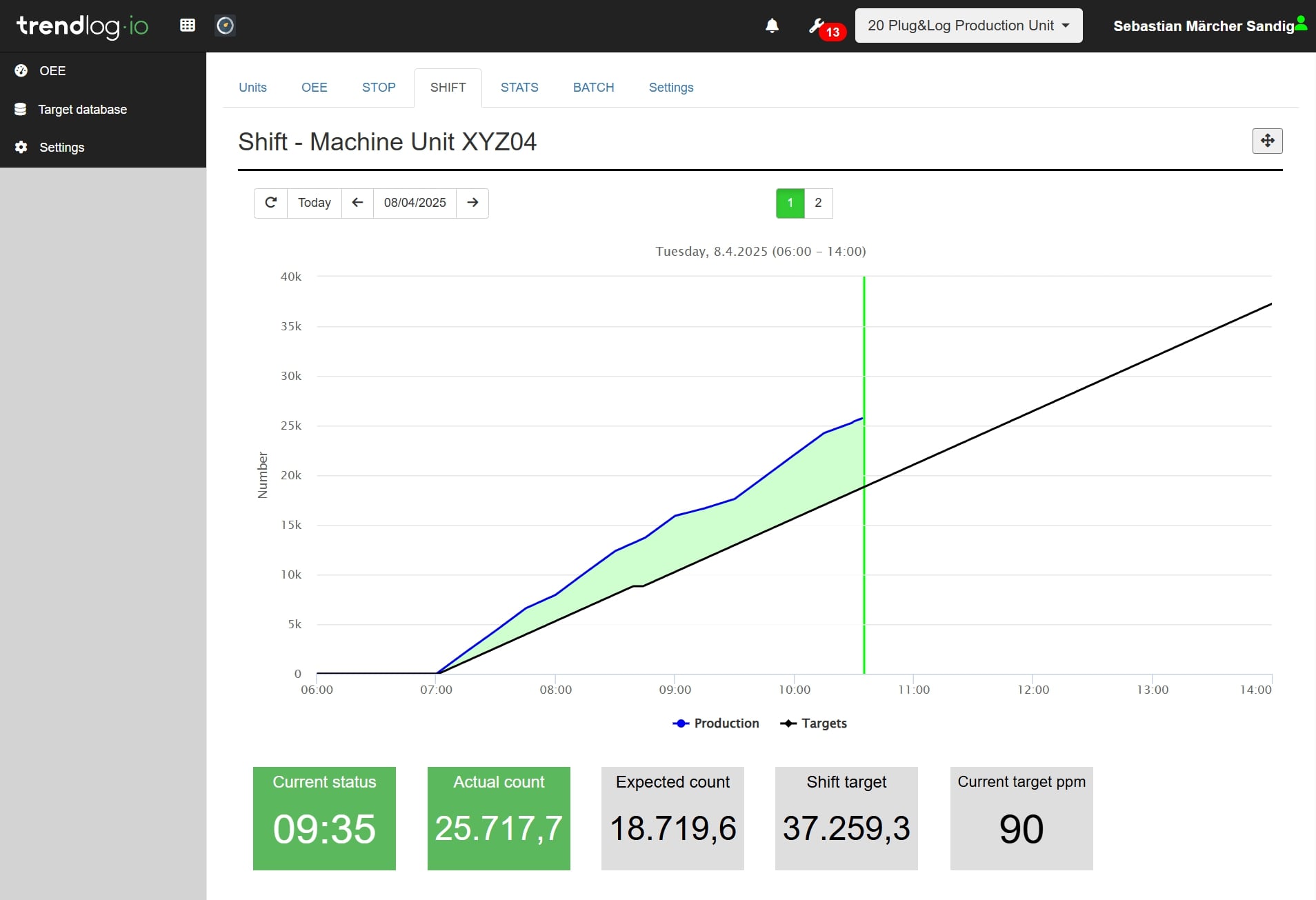
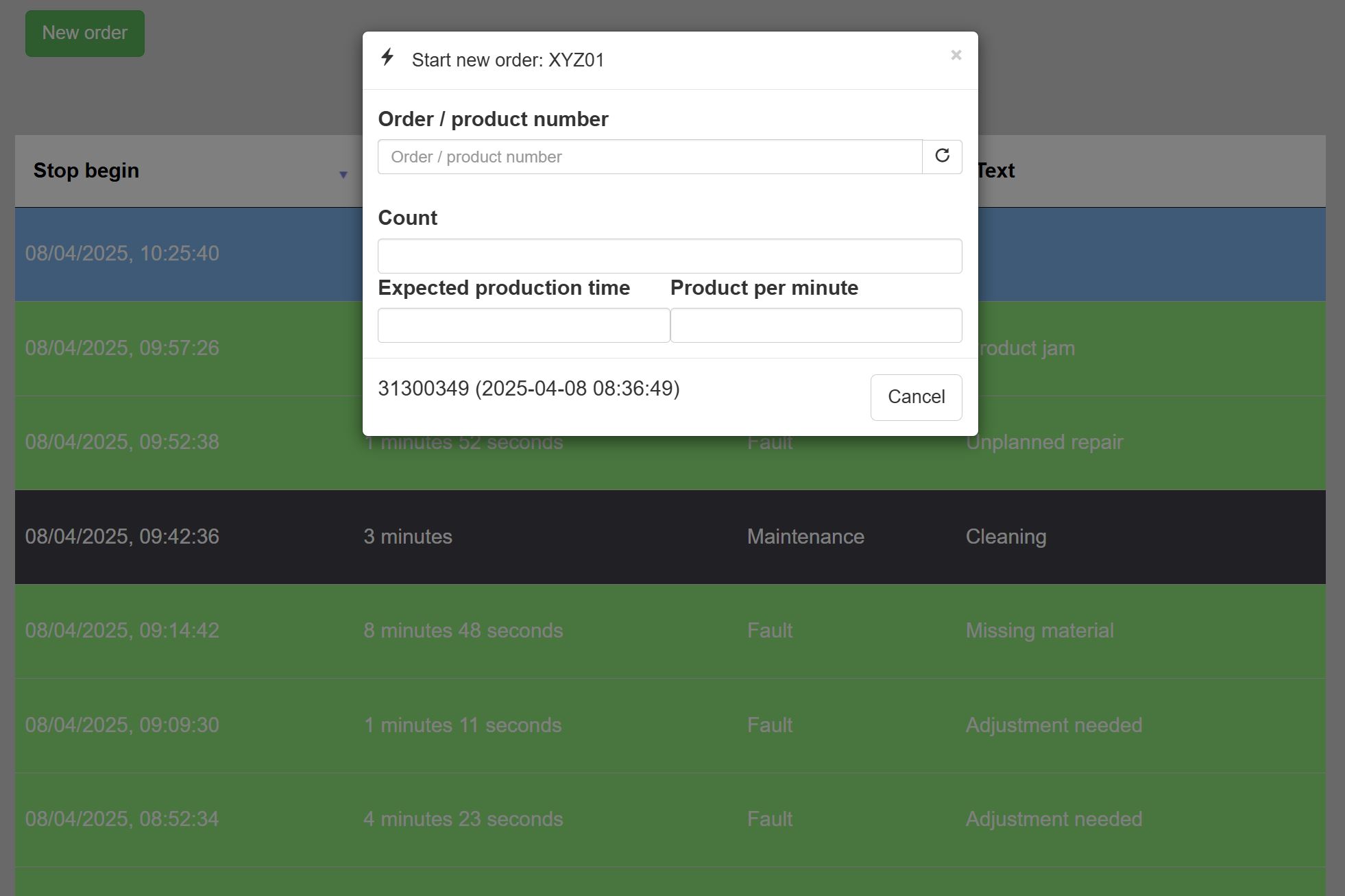
Order planning integration
Order tracking
Integrate your production orders via tablet, barcodes, API calls from your ERP system, or manual inputs – and monitor output, stops, waste, and efficiency for each order. This creates alignment between planning and reality – and documents performance.
Shift changes and benchmarking
Compare shift performance
TrendOEE allows you to define shifts and track performance per team. See how different teams perform – and enable smoother handovers between shifts with notes on orders, faults, or machine issues.
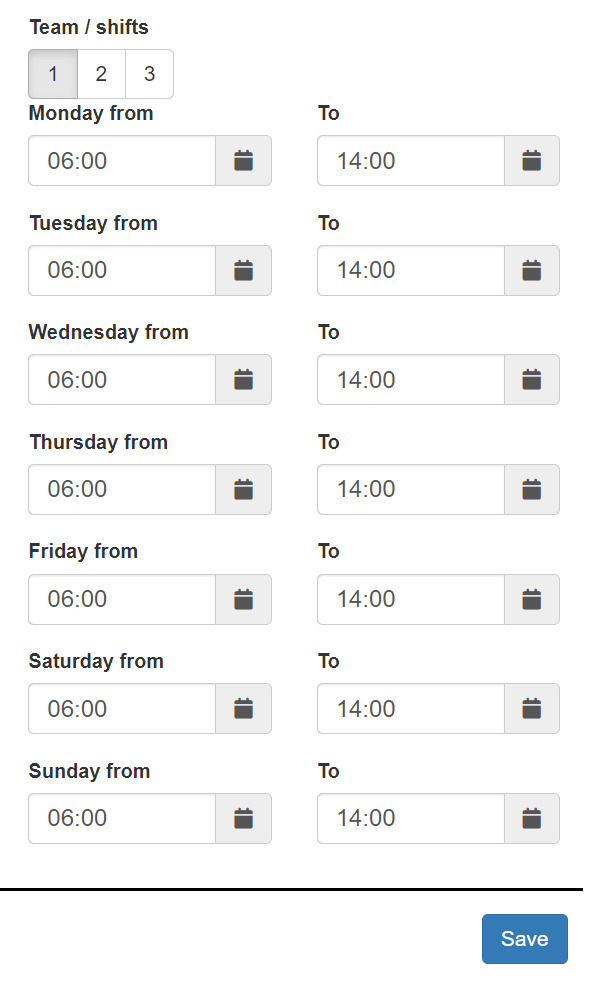
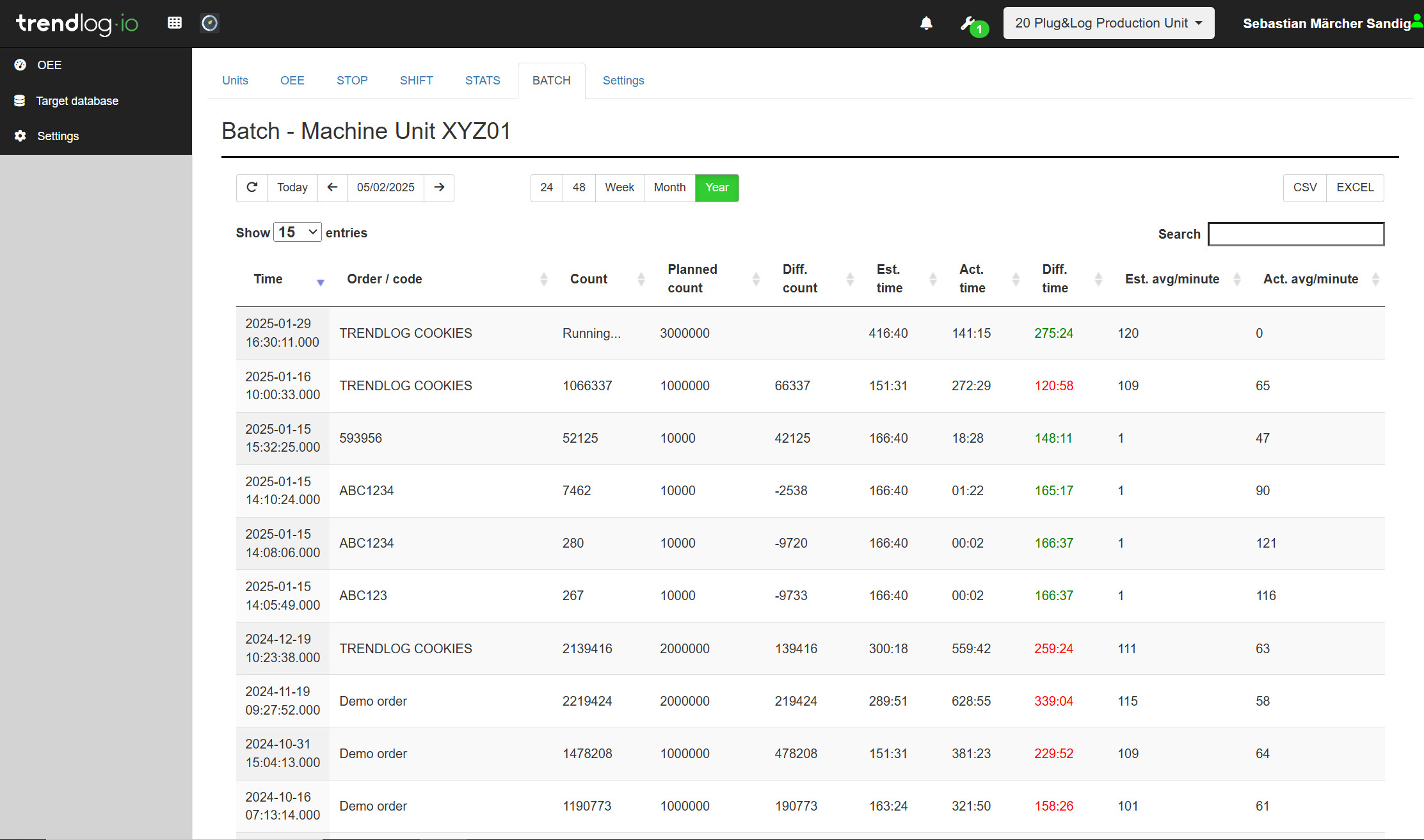
Reporting and analysis
Track actual order performance
Automatically generate reports for each completed order: How long did it take? What stops occurred? How much was scrapped? TrendOEE gives you clear, data-based answers – so you can learn from each process and optimize future ones.
All-in-One Solution
A part of TrendOEE
This feature is fully integrated into TrendOEE and the broader Trendlog.io platform. That means your data is automatically connected with stop causes, maintenance, energy consumption, and quality control – giving you one complete overview.
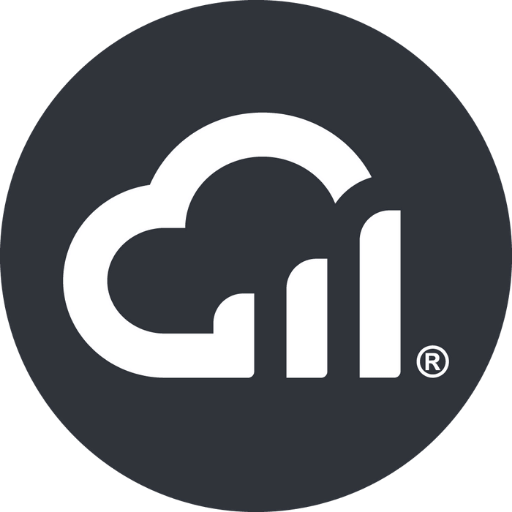
Frequently Asked Questions
How can we track performance per production order?
You can link orders to each line and measure actual vs. planned output, efficiency, waste, and downtime. This gives you order-level insights across the entire production.
Can we compare planned vs. actual production time?
Yes – you’ll see how long each order actually took, including delays, stoppages, and reasons for deviation. This supports more accurate future planning.
How are production orders imported or created?
Orders can be imported via ERP integration (API), entered manually, or scanned via barcodes on the shop floor. Trendlog supports all input types.
Can we compare performance between shifts and teams?
Yes – Trendlog supports shift tracking, allowing you to compare performance between day, evening, or night shifts for the same order or process.
What kind of reports do we get for each order?
You can generate automatic reports with key metrics like output, waste, stoppages, and actual runtime. These can be used for follow-ups, audits, and continuous improvement.
Ready to take control?
Book a free demo and get a walkthrough of how you can track performance per shift and order – and use data to optimize your operations, flow, and planning.